Screen Dynamic Vibration Analysis
Leading technology vibration analysis provider, JD Alpha Services offer an in-depth vibration review of all sorts of Quarrying equipment.
By offering flexible packages to suit your individual sites or multiple sites, we have been able to various blue chip companies to the growing list of clients.
What is vibration monitoring?
We perform vibration monitoring in order to identify changes in the general vibration levels of rotating machinery. This includes components like fans, pumps, turbines and motors, to monitor condition and performance.
We categorise these vibrations into different levels of intensity, frequency, and amplitude. We then use these to identify whether the vibration is damaging to the machine and its components. In addition to whether it is creating harmful noise emissions. From this, we can identify the cause of vibration as well as to perform any necessary repair works to remedy the fault and extend the lifetime of the machine.
What can vibration monitoring detect?
-
Misalignment
-
Imbalance
-
Gear issues
-
Looseness
-
Resonance
-
Electrical faults
What can vibration monitoring do for you?
-
Improve the reliability
-
Increase machine lifetime
-
Predict future failures
-
Minimise downtime
-
Maximise productivity
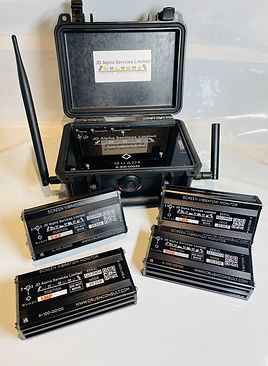
What causes mechanical vibration?
Imbalance
Obviously, If left undetected, imbalance can cause major damage and failure to rotating machinery. A centrifugal force is created when a ‘heavy spot’ in rotating equipment revolves around the machine’s axis. This imbalance becomes greater as the rotational speed increases therefore increasing machine vibration reducing bearing life and causing structural damage in severe cases.
Wear and looseness
As components such as roller bearings, drive belts or gears become worn, they can cause vibration. In addition to this, loose bearings can cause serious damage including wear and fatigue to bearings and bearing mounts as well as shaft and the surrounding structure.
Misalignment
Vibration is often the most effective indicator of alignment issues. Misalignment may be a result of incorrect assembly after maintenance, thermal expansion or the shifting of components.
Detecting the problem before it’s too late
Effective vibration analysis is essential to maximising machinery uptime, and regular monitoring can ensure this by detecting issues in good time before they potentially have catastrophic consequences. Therefore the reduction of vibration through proper dynamic balancing will help ensure the machine operates smoothly and reliably.
Example report available for download:

